|
汽车空气弹簧支架的优化设计
( h3 ~4 g! Y$ s0 ~- Q+ G W( GSolidworks作为国际上主流的设计软件,除自身提供了便捷的三维设计、装配和工程图等功能外,还集成了较多CAD/CAE/CAM应用方面的解决方案,这样便于设计人员在SolidWorks统一的软件界面下,完成整个产品的结构设计、性能分析和加工制造等产品设计验证与制造的开发流程。
% ? z! l* R9 Y# y 下面是SolidWorks COSMOS在汽车行业的一个分析案例。汽车空气悬架系统采用空气弹簧代替传统的钢板弹簧,可以大幅度提高整车的舒适性、平稳性和操纵性。笔者在对国内某款车型进行空气悬架改装时,应用SolidWorks软件进行产品三维设计、装配及干涉检查,同时采用其集成的有限元分析软件COSMOSWorks进行多个关键零件部件的结构分析与优化,有效保证了产品质量,整个设计周期缩短了30%;最终实现装车一次成功。面向设计的优化流程本文以空气弹簧某支架的优化设计为例,介绍其在SolidWorks中的优化过程。9 i' h* j2 y0 K/ o" q
1.设计要求* S% t" z- p0 t) ~
(1)在满足空气弹簧工作空间要求的同时,不得与周边物体有装配干涉和运动干涉;
; J: j& x& l! {8 l* u (2)结构的静强度满足气囊最大承载能力的要求。 对于要求(1),可以利用SolidWorks的三维造型和装配体的干涉检查等功能完成。如果结构复杂,且运动状态不易判断,还可以借助SolidWorks的物质动力功能或者集成的运动仿真软件 CMOSMotion来完成,这里不做介绍。
- [# C5 R* p, m5 [1 h 2.分析过程7 w7 ]* v' T) r) G: ^6 P# j
首先利用SolidWorks的三维造型功能,确定空气弹簧支架的基本结构,如图1所示。该支架的材料为Q345B,厚度均为6mm,零件质量为3.56Kg;然后利用COSMOSWorks进行静强度的分析,对设计进行验证。由于任何分析软件都无法做到真实工况的仿真模拟计算,所以在建立研究课题前,我们会找出影响该部件的主要约束条件及载荷。COSMOSWorks在分析前处理阶段所提供的参数设定非常丰富,基本满足大多数的案例分析:同时在模型网% q( X+ ^% C0 I2 j& e
格划分即离散化处理方面更加智能,无须手工调整网格,并且具有快速的结算能力
( J. a& @$ L, d* P. p F) u9 d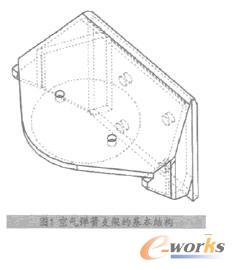 ; L) s5 H a$ _
( J, b3 V% e6 b" d) `. L6 I$ ^ 在空气弹簧最大工作载荷作用下,支架的最大应力为559MPa (见图2) ,最大位移为3.6mm(见图3)。而材料Q345B的许用应力要求不得超过280MPa,焊缝区域小于230mm。因此,基本结构的应力计算值已是材料许用应力的2倍,必须对结构进行强度优化。根据设计经验,我们首先将板材厚度由6mm增加到8mm(板材10mm厚已没有布置空间,不再考虑),重新计算,两者之间基本结构强度的分析对比见表1。当板材厚度增加到8mm厚时,其计算结果分别如图4、图5所示 |
|