2017-05-03 徐昌煜 问鼎模塑 ! A0 D1 e9 w _! K, G
5 I" b! V4 y% j
 微信扫一扫
3 l" N" H, J6 c) o k关注该公众号 - P A/ g7 P$ ?4 n4 |! P+ W0 n
! u3 c- `4 b( I, Y* W7 |5 d( Y: K
左者右之,右者左之,预变形之谓欤 ? 徐昌煜 2017年5月1日 这几年,预变形(反变形)是一热门议题。 让我们参照下图和《模具工业》2008年第34卷第4期中的一篇文章”变形预补偿在降低注射制品变形中的应用”对预变形的描述得很好,可作为探讨预变形的开始。 “变形预补偿的原理如图1所示。 在制品上选取一条曲线f,r为曲线f上某点r的位移矢量,在三维模型上曲线f的位置为f0,点r的位移矢量为r0,制品发生变形后曲线f的位置为f1,点r的位移矢量为r1,点r的位移矢量的变形为Δr1=r1-r0 。 曲线f2为变形预补偿曲线,点r在该曲线上的位移矢量为r2,相对于原始曲线,点r的变形为Δr2 = r2-r0。 如果在制品模型重构时,将曲线f的位置移至f2,且Δr1与Δr2满足如下关系Δr2 = - Δr1,则可使制品的变形量降低至最低。” 模具工业2016年第42卷第5期中有一篇文章”塑件预变形设计方法与应用”,能够分享其预变形的作法和经验,实属难能可贵。 且看如下报导(徐昌煜老师(C.Hsu)的点评则以蓝色字体标示): 塑件预变形的方法 预变形是利用CAE分析的塑件变形量或实际塑件变形量对塑件进行预变形设计(反向变形),从而改善成型塑件的尺寸。 利用预变形后的塑件(C. Hsu:模腔)数字模型设计模具,塑件在出模时经过内应力释放和各向收缩,产生一定量的正向弯曲,从而达到生产的塑件与设计要求一致的目的。 塑件预变形补偿的原理是在尺寸减小区域增加一个反向的变形量,在尺寸增大区域减少一个反向的变形量。 通常塑件由于结构原因各部分的翘曲变形量不同,需要将塑件各不同区域的翘曲变形量进行反向变形设计并附加到客户设计的塑件(C. Hsu:模腔)数字模型中。 --- 模具设计之前,通过moldflow软件模拟分析塑件(C. Hsu:几何造型应为模腔造型而非塑件造型) X、Y、Z 3个方向的理论变形量及主要变形原因,综合考虑客户要求, 塑料材料的物性参数,模具浇注、冷却系统结构,注射工艺参数,并结合积累的各类塑件的成型经验,计算出塑件X、Y、Z向的预变形量,在尺寸增大区域减少一个反向的变形量,难点在于Moldflow模拟分析的准确性及预变形量的确定。 案例分析 某车型的尾翼(见图1(a))壁厚均匀,基本料厚为3.5mm,1,175 mm x 87 mm x 167 mm,塑件质量455g,材料选用PC+ABS T85 x F。 根据材料的流长比计算,选择7个点浇口进料(见图1(b)),按默认工艺进行初步分析,具体工艺参数设置如表1所示。 --- CAE分析对比不同工艺参数的影响 通过调整注射工艺参数,包括模温、熔料注射速度、型腔保压压力、熔料冷却时间等参数(由于影响较小未计入表格),统计塑件两端的实际变形量(见表3)。 由表3可见:在浇口结构、模具结构固定的情况下,调整浇口的打开顺序和模具温度,成型塑件的变形量差异在±1.5mm,无法根本解决塑件翘曲变形问题。 7个点浇口不同进料方式的模拟分析' E: I. Z3 s( S8 y8 \ G3 m
/ d! P& y6 P4 U5 J6 T7 P( E
在工艺参数设置不变的前提下,通过对设置7个点浇口顺序进料和同时进料方式进行模拟,塑件X、Z向变形量模拟结果如图5、图6所示,塑件实际变形量如表4所示。 C. Hsu: 实际变形变化量与模拟变形变化量差异太大时,模拟结果难为依据,若方向相反则切不可用。 否则治丝益棼,徒劳无功。 表4的实际X向变形量与图5的模拟X向变形量方向似相反,若是,模拟变形量不可作为预变形的依据。 由图5、图6和表4可见:7个点浇口顺序进料对塑件翘曲变形影响相对较小。 考虑到塑件为外观件,根据材料供应商推荐的成型温度,选择动定模温度65°C,7个点浇口顺序进料的CAE模拟結果,塑件X向变形量5.4mm,Z向变形量11.1mm,根据经验,塑件的预变形量选CAE模拟变形量的3/5作为预变形量。 C. Hsu:表4的实际X向变形量与图5的模拟X向变形量方向似相反,若是,模拟变形量不可作为预变形的依据。 模拟变形量的3/5作为预变形量或有疑义。 --- 在确定好塑件的预变形量之后通过专业的CAD软件对预变形塑件进行结构设计,将留有预变形的塑件与原塑件进行模拟分析,留有预变形塑件与原塑件成型后的变形结果如图10、图11所示。 由图10、图11得到验证:用PC+ABS T85XF材料,7个点浇口顺序进料对留有预变形塑件与原塑件成型进行模拟分析对比,两者变形量均较小,可以推测留有预变形的塑件变形趋势,变形量与原塑件的成型变形趋势、变形量基本一致。(C. Hsu:但是,留有预变形塑件变形量并未减少。) 留有预变形塑件实际试模成型的X,Z向尺寸误差均在0.5mm以内(见图12、表5)(C. Hsu:但是对留有预变形塑件而言,实际与CAE预测的变形量差异太大 !)。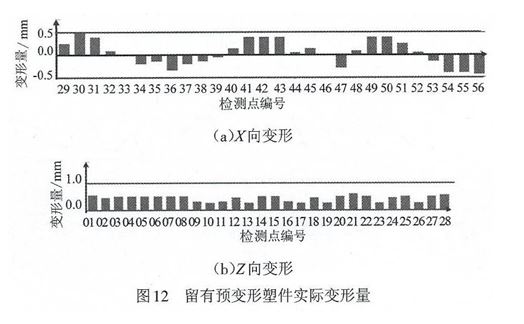 4 P; F, k* g: K* I9 a
3 K/ q/ s1 `0 W7 Y! ]
4 v4 N* Q3 _) m0 o; ?# q: F& I |