1.工件寻边偏差或错误.
0 c; y) N9 x: X% z/ p+ J" n$ o 2.(1).现场人员疏忽.
0 h2 q. v1 S9 g5 y/ { (2).图面尺寸标示不清.x. y. z未按惯有方式标注. (3程序单加工原点与图面原点不重合. 2.刀具用错或程序单写错.(在程序copy时经常出此错误.) 预防措施: (1)编写程序之同时填写成程序单.
# c) P" @4 X+ P& K9 q/ p5 }( n(2).程序写完之后须一一核对刀具之大小.
- Y+ x+ d# L* q% B
(3).将程序号码及使用之刀具大小手动加该程序NC码之开头. 例如: ) ?3 a4 i% ~& ]+ L6 t9 R- ]
23M130.CNC,其程序使用之刀具为Φ12R6的球刀.那么该程序NC码开头应排列如下: O001.% ) y) ]' v) F- x/ P2 R
O002.[23M130.CNC,D12R6]
* F2 b: |- Q8 N: v4 b6 f3 eO003.G90G00X0.0Y0.0
" Y* z5 Y) k, `5 I" k
O004.G00Z150.0
& ^" U2 L( b0 b! L1 I) \4 SO005.----------------
3.粗铣时裕留过少或刀具Φ径不准. 预防措施: (1).程序设计者应对刀具之切削性能及材质须深入了解.根据实际情况进行裕留.
, S' q5 y: V. P$ t' I: U. d( h! p! P(2).装夹刀具前必须对刀具进行准确的量测.
$ j6 g( ?4 ^+ s& A# ?
参考考标准: Φ代表刀之直径. 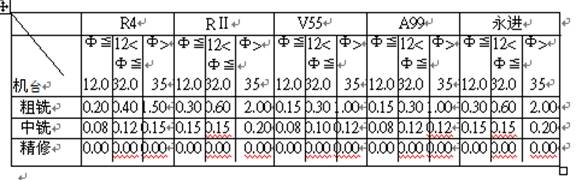 2 G# _ _0 P& @" p7 P' z) l0 n: j
4.刀具装夹不牢或伸出过长产生过切:
( M- T1 R% P3 l8 L; E2 L预防措施: 1.装夹刀具要牢固
2 M: C \4 o8 u! U9 h* V2.刀具伸长一般不超过刀具总长2/3.
* `. Q6 B0 \$ d( z' w X* t+ l
3.刀具在特殊情况下必须延伸(超过2/3以上).切削量须相应减少速率和转速也须降低.
( n7 j. S# B/ C' e, B5. 切削量过大造成拉刀过切
(1)在切削时加工者应考虑到工件的材质及硬度.刀具及机台之刚性进给量以及转速的调配 参考之标准+ Y! ~, S: ` x1 U. H
TOOL
( A, y6 Z( O) d }XY2 i- o( j9 j* m- ~/ y3 P; |
Pitch/ ~. U$ o8 j' O
Z
D; ^+ ~, l) n- h+ n0 JPitch  
; J$ d- k5 T4 w0 m$ rΦ32*R0.8! j( \" b8 H/ ^3 J0 `# V* i! v9 r
1 P0 z0 z2 V( V' S N# Y
45%~75%
. Z2 q. g8 i A/ h8 r. O& e; D(3~5)mm
! ~. O) _. N& Y; w# |7 L* C0 c
舍弃式5 e/ U0 }1 L, a1 M1 _" { f
Φ25*R0.8$ @3 j: g. L3 a1 B/ E- u5 S, [
45%~75%
: i8 B+ p6 R3 x `4 Z I(2~4)mm ; }% x `" ?! J) ^
Φ16*R0.48 s+ O v3 f% Y" |6 b
45%~75%" l d* N0 x; _) K' f
(0.5~2)mm
) B9 \8 F$ d; k5 r' p! y粗逃 # \/ A' S q( X; Y7 a3 |
面铣刀
, a8 k8 i. L: g' p1 F9 _Φ68*R0.8
. O& G4 B/ a, k8 t! D50%~75%" I/ A/ _1 D# V
(3~6)mm
8 }/ P" Y6 Y+ w
现场因调错程序而造成过切 预防 a)现场应按照程序单上指定Path进行抓程序
9 I" h" _4 O+ D( A3 L(b)现场应对程序设计课之作业第统及程序代码之编码原则进行了解
程序代码=模号后两码+工件代码(两码)+电极序号(若用电极)+程序序号 例如:
: k4 z- D7 p. E7 ^. y* |23 M1 EA 01         2 c$ i% p8 ?' F0 @7 n. z
程序序号(2码)

6 [* w& c, d* H, p电极之代号(2码)
: V* |+ C9 v8 z
工件之类别及代码
: `7 Y6 N! q4 j3 F/ u- n
模号
(7).程序写错误(例如:边界裕留量Floor面输入错误) 4 V N+ ?* Z* A) O ~
- - - - - - - - - - - - - - The) d. B+ Y* S. n9 f
End - - - - - - - - - - - - - - - - -4 }9 a: c' Y/ u4 S, I. v
% D- v n' N4 X
/ K F' n5 i: S) `2.刀具撞刀原因
8 @7 J1 R( ?) a(1).NC码编写错误
7 @0 c7 \$ y8 L9 b% F例如:工个之零点在最底部或工件的中央而不在工件最顶面.程序写完post后.-而post后理程序之内定高度为=50.0
5 g- A0 }, @, h工件之需点与最高之顶之距离50.0时工件可能或撞刀
(2).刀具测量不准
5 V2 ]5 C7 g1 \. M) J预防措施:刀具测量尽可能用较精确的义器
(3).程序乱码(由于传输错误造成的撞刀). 程序号码呼叫错误或程序有修改但仍然用旧的程序进行加工与编写日期 程序单设变时应采用以新换旧之原则将旧的图现及程序单应消毁 现场加工者尽可能在下面碱查一下程序之详细数据 例如程序之容下程序之时间和日期
7 q1 z1 d6 q: B% u# ~, x(4).刀具用错或程序单之刀具写错 预防在该程序之程序头追加备注程序之号码及刀具直径如第一页 (5)安全平面设定不够高刀具没有让开到就移信以致撞刀 # ?- V Q' s+ s" D" i
例如: 一把刀在做多个部分且两个部位之间凸起之岛屿之加工时﹐为节约现场提刀之时间﹐设定两个安全平面﹙较高的安全平面大于工件之最高点﹒较低之安全平面低于工件之最高点而高于要加工之部﹚﹒当刀具加工完一个部位之后提至较低之安全平面﹙由于软件之局限性﹚准备加工一个部位时﹐中间提刀越过凸台由于高度较低于凸台而产生撞刀﹒ 预防:A.程序写完之后应对程序之路径进行模摊﹒ % }0 y+ F, V) x5 i2 z1 N
B.针对上面之问﹐若要缩短现场加工之时间﹒必须对各个部位之加工程序5 B* b, |# B3 d1 {
/ | I( B; [9 b/ }6 _! O/ P分开写﹐然后POST在一起﹒
1 B/ L& H$ N! B gC.刀具拉出工件之距离不够﹐使刀具直接插到工件﹒
& e! w' V% o8 I: [( [" _0 E
预防及参考标准:刀具进刀拉出之长度应大于刀具半胫 ﹙6﹚程序之备注考虑不周祥
8 ^3 B9 Y! G2 B7 _! O1 w1 Y" v# A; P" m* q& [7 a
例:A.工件凸出虎钳之高度不够
' D( f' F/ n" K) Q2 e# C' B6 X
B.吊螺丝时夹螺丝时荡围小于刀具路径运动荡围时导致刀具撞到周围的螺丝 1 Z( z. x7 H) g, T% k
C.刀具备注时伸长量备注不祥或错误时会导致撞刀 ﹙7﹚残料不均匀 ﹙8﹚工件材料本身有缺陷或硬度过高 ﹙9﹚垫块位置过高程序中未考虑装夹之因素. ﹙10﹚残料不够均匀而引起撞刀﹐编写加工程序时未考虑到余残料分布是否均匀﹔
' p8 N4 e, I0 x1 a" F. K @8 X* n
) k% z1 y) M; ]2 q就改换小刀修时易撞刀﹒因为加工时进给及转速恒定情况下一旦切列厚料﹐% f0 j% L" p0 q% }9 ?
% O2 N, z/ Q# |5 k# ?" T& H# K
冲击力必增大而造成打刀﹒
4 l; v# ~0 F/ N* ?1 ^2 c% ~预防: (1)大刀整体粗逃后切记用小刀清角.
0 K: L$ R: N( @" D$ K$ @
4 q6 q: U! K4 a/ ^" x. N A4 y# }
(2)在小刀加工前确保工件表面剩余残料为均匀之分布﹒ |