|
发动机气道曲面反求及其模具设计+ D! w' w. `5 r, `/ T( ~
快速原型技术(Rapid Prototyping,简称RP),就是借助计算机辅助设计,用曲面反求的方法采集得到有关零件的几何形状,一次性建立数字化扫描模型,达到快速、准确的制造信息零件的现代化方法。RP技术是当今世界上发展最快的制造技术,是近20年来制造技术领域的一次比较大的突破,是先进制造技术领域的重要前沿课题之一。RP技术的特点是由CAD模型直接驱动快速制造任意复杂的几何形状,基于这种方法,我们实验室实现了桨油机进排气道模具设计和加工。' s% {+ |( R/ a5 L) z
发动机进排气道形状是影响发动机功率、扭矩、油耗、加速性能、排放、振动及噪声等性能指标的重要因素之一。但其几何形状极不规则,难以用二维几何图形及数学解析式准确表达。目前,国内引进的发动机很难获得进排气道的原始三维数据,通常是在二维图上表达几个截面,再提供一个或几个样品,难以直接根据产品功能和用途正向进行气道三维造型和模具设汁制造。传统的方法常需制造样板经过反复的试验与修改,导致了产品精度低、模具尺寸形状重复性差、开发周期长,最终导致发动机性能不能达到要求。为此我们在气缸念些排气道摸具设计中引人快速原型技术,使进排气道模具设训和加工实现数字化。
, i4 x9 @1 V8 M4 I, F 我们主要是通过实物反求(RE)获得表面数据,然后在CATIA环境下实现逆向实体造型,将处理好的模型保存为通用文件格式,在Pro/E中进行模具设计,最后调人数控加工软件MasterCAM中进行NC加工,由MesterCAM后置处理模块生成NC代码,下面以柴油机排气道为例说明其加工和设计过程。+ c/ } T+ t* i( u0 n) ~2 A
1 排气道模型的表面数字化
3 }5 L' h$ O3 ~2 ~ 采用无接触激光仪扫描排气道表面曲面,可对排气道的不同位置区域进行扫描,把测量结果直接变换到目标坐标系,基于测量系统提供参考点进行拼接。测量系统本身自带软件可以对点云数据预处理,如:进行去噪和均化、冗余数据的压缩和归并、残缺教据的平滑填补等处理,以剔除无用有害数据.保留并优化有效数据,减小测量误差对三维建模精度影响,测得的点云数据以标准格式输出。经整理后的点云数据如图1所示。; N5 z5 u3 Q E) n
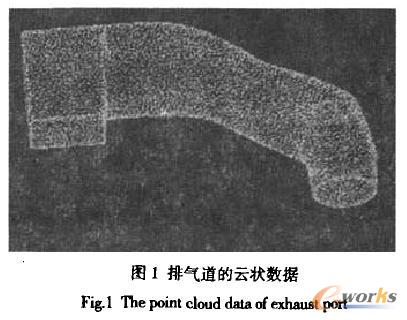
排气道的云状数据
* A( x$ |: d0 v4 \. `3 {5 k, j/ Q! _. e% A
2 三维模型重构
% ]+ ?/ K2 e; H# l0 ] 曲面重构的关键就是根据大规模散乱测点数据,重新构造具有复杂曲面外形产品的三维计算机模型。从工程观点评价曲面重构的重要指标是模型的精确性、光顺性、几何不变性及对大规模散乱数据的重构能力。排气道的曲面重构及实体化造型是在CAT1A环境下完成的,其曲面重构过程:c1>特征面识别。将点云划分出若干个特征区域,用不同的颜色加以表示;(2)点云分块。根据自动识别的特征区域,将数据点云分成若干小块,以便分别处理;(3)分块重构特征面。对点云分块分别进行重构,得到许多独立的三维曲面组合起来,通过倒角、缝合等操作使其光滑连接;这里要解决的主要问题是曲线的创建和诊断修改.只有满足曲线光顺,曲面才能光顺,曲面与点云的吻合精度也主要靠曲线中关键特征线的提取和创建精度来保证。(4)曲面误差分析。对已完成的曲面,进行曲面误差分析,以在设计要求范围内
" } ]% w/ ], `控制拟合曲面与点云之间的误差≦0.lmm),最后完成由曲面向实体造型的转化。: g8 D- k! v. _9 k8 @5 O7 f' t
3 排气道的模具设计
/ a' \6 u: O1 M7 O: x4 A) K" o9 W; f 3.1 建立模具体积块- U/ h, g- H5 [
将排气道在CATIA中另存为通用文件,然后将导人在通用文件Pro/E中打开.利用Pm/E数控模块中CATING(铸造模具设计)子模块进行模具设计,使工件坐标系和模具坐标系一致,生成参考模型,用手动方式建立工件体积块,"按尺寸收缩"方式去设置收缩率。设计加工铸模浇注系统时,要使浇注通道能够控制金属液充填铸模型腔的速度及充满铸模型腔所需的时间,使金属液平稳地进人铸模型腔,阻止熔渣和其他夹杂物进人铸模型腔等。4 A: u' C {/ @: p! o! |
3.2 排气道的分型面设计9 R6 _; Z3 Q5 j8 ]
设计分模具分型面的用处主要是用来分割工件,从而生成用户希望得到得体积块,分型面选择的合理与否,对造型工艺、铸件质量、工装设备的设计与制作有着重要影响。分型面的选择要在保证铸件质量的前提下,尽量简化铸造工艺过程,以节省人力物力。在选择分型面时要考虑以下原则:分型面的选择应保证模型能顺利从铸型中取出,这是确定分型面最基本的要求。因此,分型面应选在铸件的最大截面处。应尽量使铸件的全部或大部置于同一砂箱,以保证铸件的尺寸精度。为便于造型、下芯、合箱及检验铸件壁厚,应尽量使型腔及主要型芯位于下箱。Pro/E模具设计模块提供了多种建立分型面的方法.根据上述分型面的设计工艺要求结合气道的结构特点,产生的分型面如图2所示。 |
|