今天我要和大家探讨的高速加工是狭义上的基于PowerMill的高速切削技术。广义上的高速加工我不在这里讨论,因为它包括了高速加工机床、高速加工中的刀具技术、高速装夹技术、高速的CAD/CAM技术、高速切削技术、高速冷却润滑技术等太多的东西。
: i3 h7 W6 N6 z: V; B4 _( q$ f* a5 L" i& y$ Y
* v6 w& C* V9 O; {# A4 i U要讨论高速切削技术,我们必须明白高速切削技术的目标是什么?从技术层面来说高速切削技术的最核心目标就是让加工工件获取最佳的表面质量和最高的装配质量。怎样获取最佳的质量?这意味着在切削过程中要保证切削对材料结构的损伤减小到最小。单从高速切削技术考虑,目前比较流行的研究结果为:刀具很大的切削线速度和平稳的较小的切削受力能够保证减小切削对材料结构的损伤。因此单从高速切削技术上来说要实现高速加工,就必须要达到精加工前工件表面的余量充分均匀和余量尽量少,我们一般称为"等余量"和“轻切削”。这个条件如果要用工程师凭经验手动控制,将变得非常繁复且劳累,由此可见一个好的CAM软件粗加工策略必须智能地为精加工创造条件,而PowerMILL在这个方面做的非常出色。
- `: }9 R1 M6 x, E& B: _$ @. T
二、PowerMILL智能化的粗加工 - V4 b, _: `3 e0 C' t
PowerMILL智能化不仅仅得益于Delcam现在拥有世界最大的CAM研发团队,更重要的是得益于Delcam公司自己的大型数控加工开发车间,该车间任务多来自于世界顶级的航空航天企业,细节关注度非常高,实战性非常强。PowerMILL所有加工策略都必须通过车间长时间实战测试,安全性非常高。 8 K. F+ i# j' N6 f6 }6 b3 E
在这里主要对PowerMILL的开粗策略的细节关注度通过一个实际例子讲解:
2 N- t0 Z' n B, t8 X0 l c 样板工件: 前格栅后模(注塑模具)* h6 y0 B s5 I0 c$ V j
特点:工件梯度很大,滑块槽和斜顶槽位多
5 Q. j3 A9 _5 A5 [! P 加工规划:工件梯度很大,开粗刀具要短、长结合提高加工效率$ h/ a# y& Z! }9 s
滑块槽和斜顶槽位多,且槽的大小形状不统一,要用到多刀清角 & k) T+ M7 F! F
难点:刀具要短、长结合对CAM软件自动碰撞计算和刀路碰撞检查要求很高 多刀清角对CAM软件的二次开粗的安全性和计算能力要求很高 , w6 @. L6 @$ K6 u. i' |8 h( [
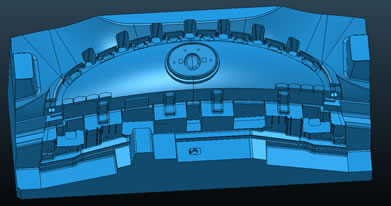 & W2 K) F9 B, G! {7 q: T& C

7 ]- P+ {) P9 W' c, K智能细节一、PowerMILL自动碰撞计算
4 b2 [, Z# h7 p2 a: `工件高度为395,开粗短刀设置为长度180,这就涉及刀柄和机头的碰撞问题,PowerMILL可以轻松解决。
! i5 K, j" j" t; p" ~4 l2 ?0 }方法为:先把刀柄、夹持和主轴头在刀具面板设定好(有刀具数据库的可以直接调用),再把加工策略面板中的“自动碰撞检查”复选框选中,间隙数值大于开粗余量即可,这样在计算中PowerMILL就会智能计算并保持刀柄与工件不发生碰撞。 8 D! P2 \8 T6 v# j E* ]
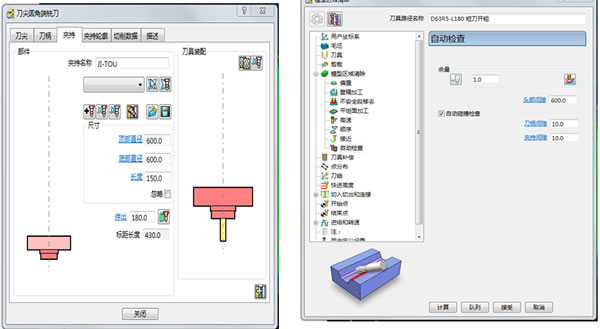 ; p7 L% @5 p6 J. j4 M0 B$ J
D63R5-L180 短刀开粗结果如下图: $ e7 A: t: V& W0 _6 Q
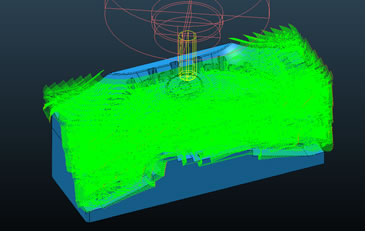 ( O( M2 Z& _* O7 Z! c; j$ Y! }3 s: p+ B
ISO视图可以看出: 短刀深加工在PowerMILL中发挥得淋漓尽致 ' c" X( y; ?1 z1 Q' m
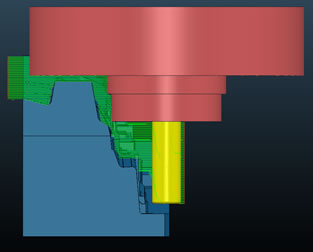
, y- M; G2 c+ k* U* o; ^0 ^侧视图可以看出: 夹持任何一个部位检查距离小于“自动碰撞检查”数值,刀路将不会计算出来
4 v! [4 F. u2 {) L) b: ^' Z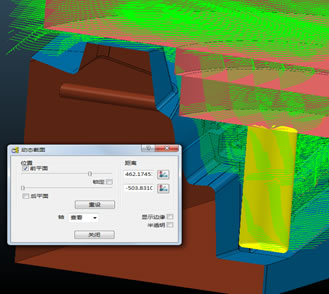 ) p( T: }& F6 M6 Q' c, ^5 C7 b
从PowerMILL的动态截面剖视图我们可以更加清楚看到这个“自动碰撞检查”的安全性和准确性。 ( R, M4 V3 B+ @* i) t; l4 y
智能细节二、PowerMILL残留加工
u$ P- L+ z2 t5 S+ `残留加工实际就是自动、智能的识别前面刀具切削后的状态并根据这个状态进行后续刀路计算。粗加工策略中PowerMILL残留加工提供两种方式,分别为为“刀具路径”和“残留模型”。“刀具路径”实际上就是参考某一个刀具路径进行计算,但这种方法局限于三轴加工且只能参考其中一条刀路计算,我不在这里讨论。
8 b' _2 v. m7 O; S: J- C% s
残留模型是PowerMILL特有的一个加工过程体,它能够动态的记录加工过程的毛坯信息,简言之就是一个完全支持多轴加工的动态毛坯。残留模型好处可以举个简单的例子来形容:一个苹果(毛坯)→妈妈咬掉一块(开粗)→被咬缺的苹果(残留模型)→女儿再咬掉一块(清角)→被咬缺两块的苹果(残留模型)。在过程中女儿不可能再去咬妈妈已经吃掉的地方,达到口口见量。残留模型的原理和吃苹果原理一样,可以使加工尽量达到刀刀见料。在PowerMILL 2012版本中残留模型完全贯穿所有的粗加工和精加工策略,给高速精加工切削技术带来了另一个全新的制造气息。 7 y8 G6 J' T3 k4 U
接上面例子,D63R5-L180 短刀开粗结果在残留模型中表现如下图:
# `$ V1 c/ \1 S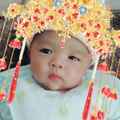
" m% E: z- K1 t可以清楚地看到粉红色模型为PowerMILL 的残留模型,我们可以看出D63R5-L180 短刀开粗结果,标记白色区域余量非常大,但由于为开放区域必须继续用D63R5长刀进行清除,标记红色区域为封闭小区域,必须用更小的刀进行清除。
. V6 m- Y ^" e) I+ _$ Y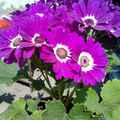
$ s4 s5 f0 W7 E7 e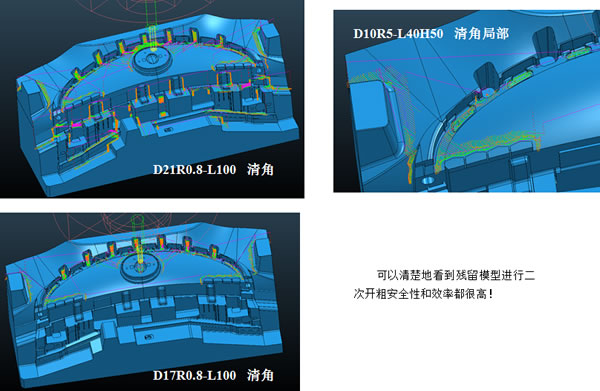
: b. X$ e: `2 D$ w通过残留模型清角刀路最后效果如下:
, R1 f& z/ g1 {4 h% M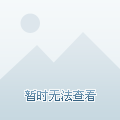 ) Y4 o+ @! Q3 S, V2 m# _7 R( ?
智能细节三、PowerMILL不安全段移除
: u8 g3 w4 \2 j7 s' l {3 w2 P不安全段移除是为了避免加工过程中区域太窄造成不安全事故发生,此类事故一般表现为轻者“伤刀动模”、重者“机毁模亡”,这类“烧刀”和“撞刀”事故后果是非常严重的。面对结构复杂的模型,如果没有智能化的CAM计算方式,编程人员往往要花大量的心血来清除刀具不安全加工范围。而PowerMILL可以自动准确地过滤掉当前刀具的“盲区”,安全进行切削。 接上例模型中斜顶槽加工,最中间一个斜顶槽位:测量结果如下: $ M% g! L# B+ w# m6 d" d
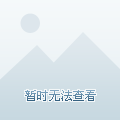
) b0 B; P# ]$ R' n" w0 o一般初级工程师会认为只要用小于直径25的刀即可,比如我们选一把D21R0.8的牛鼻刀来加工,结果如下:
0 K1 F* W% g; m( s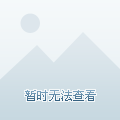
- j# a( o. `( O u) }刀具活动范围太窄,这种情况加工过程一般表现为刀粒损耗很快,容易烧刀。
, ^3 g2 P6 i+ I" v1 s+ A- X% rPowerMILL的解决方法如下:
0 f" m& N W# k) ^! W' F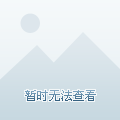 ^! V1 D9 G% ?5 |" H
在策略面板中选择“将小于分界值的段移去”即可。分界值为刀具直径百分比,一般开粗为0.6以上就好了,如果是上刀粒的牛鼻刀中间盲区比较大的话可以多给一些,个人经验认为0.8就好了。也就是说最短刀具路径不能少于0.8刀具直径。 % X' m* W7 p, }" H* t d
计算结果为:
; q: O& Q! }$ Z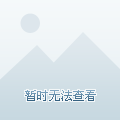
3 @; p, w2 B% k) |& @可以看出在小于刀具直径0.7的活动范围区域已经被过滤掉,也就是说在长和宽均小于21+21*0.7=35.7的区域将不会加工,而要把这个槽开粗做好我们要用多大的刀呢?方法为:槽最窄区域的最长边长/(1+分界值) > 刀具直径 就可以了,本例中最窄区域为30*25,假如我们的分界值为0.7安全开槽的刀具直径为:30/(1+0.7)=17.647 所以我们可以用直径17mm以下的刀安全的开粗出来。 2 J" D8 K, u, w4 j2 C9 K
本人在PowerMILL残留模型加工中结合不安全段移除和自动碰撞计算做出的最终刀路如下图:
0 K" ]/ i/ H! ?/ \ B- O& U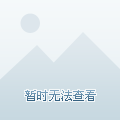 ( a5 Z1 h/ X9 F! X$ P% ~
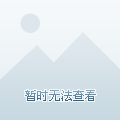
. o6 F' X# S8 ^- T4 X, b通过这个粗加工实例我们可以看到PowerMILL安全准确地识别工件特征并根据工程师给出的加工环境智能地生成优化的刀具路径过程,再加上PowerMILL对多核计算的完全支持,编程工程师可以轻松地快速有效地完成复杂的编程工作。PowerMILL可以让一个工程师从机械编程中解脱出来,用充分的时间用来规划我们的加工工艺,用更多的更好的策略来提升产品的加工效率和加工品质。总之, 使用PowerMILL的每一位敬业的工程师既是一个加工项目的管理者,更是一个现代高速加工行业的雕刻艺术家。 " Y! P: K* M* T- P8 i7 x
6 x, J- [! _7 C6 h' ]: T8 i2 h0 S编程中遇到问题需要解决的或是想学编程的# V v" \9 _* ^6 I" Z, X+ l
# Z) z- z2 M, M' E) i1 V; z
# p3 ~3 r* S1 w+ T* k# }7 X. W都可以加QQ 2772379269
- ~0 A8 o/ V( z
. A8 ]8 j- A, M. V5 R |